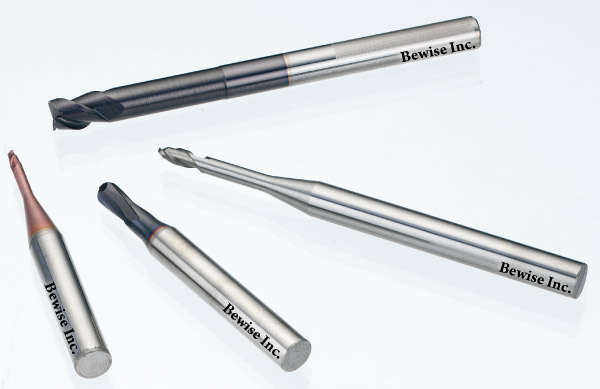
The super-hard thin film coating:
Depositing TiC, TiN, TiCN, Al2O3 ...
hard ceramic coating with a few μm on carbide tool is more suitable for high speed machining than
WC series, and with higher feed strength than ceramic. There are two depositing ways -- CVD (chemical vapor) and PVD method (physical vapor method).
Depositing methods:
depositing method |
CVD(chemical vapor) |
PVD(physical vapor method) |
introduction |
Use of the air chemical reaction, deposit coating under the temperature about 1000 ° C . |
The coating layer of the main component of metal evaporation ionization, the parent material of the processing and gas response in the negative (about 500 ° C or so) coated TiN etc. |
advantage |
1. The base material can be fully coated.
2. Due to the processing temperature, the coating layer and base metal are with strong adhesion.
3. Different coating layers can easily gas switch.
4. Low cost because it may be processed in large quantity. |
1. A low processing temperature, there is almost no heat distortion.
2. The coated particles fine petty in the sharp tip directly covered.
3. Compression stress in the coating layer so favorable strength.
4. Safe and without pollution, no exhaust treatment equipments needed.
|
defect |
1. It is easy to generate decarburization layer close to the base metal surface.
2.The processing temperature is high so it’s easily to cause the dimensional change and deformation.
3. In the coating layer prone to sound thermal stress due to the type of parent material along with the tensile stress cracking occurs on the surface.
4. Due to HCl produced, it is necessary to have exhaust gas treatment.
|
1. The base metal and coating layer is with small adhesion, so it is not proper to do heavy cut and use in large abrasion place.
2. Difficult rotation so you must use the parent metal rotary mechanism.
3. Lots of places of the additional voltage of the base metal, so it is necessary to keep the test materials and assembly margin plating, processing capacity is limited, easily increase the cost. |
|
Demand characteristics of the coating film:
- Hardness
- Wear
- Anti-melting
- Oxidation resistance
- Corrosion resistance
- Toughness
- The fatigue strength
- Thermal fatigue resistance
- Resistance to stripping
Application of cutter coating film characteristics:
The coating is just like cutters’ armor, with powerful protection, acid resistance, resistance to oxidation, wear resistance and other characteristics, can increase tool life largely, improve the surface quality of work piece, increase productivity and quality approved rate.
Coating treatment must be in proper arrangement in order to play a high-performance under the conditions of usage. Hence, we must understand the coating characteristics, and then applied to the cutting tool to achieve better results.
coating film |
TiCN |
TiN |
TiAlN |
CrN |
DLC、ADLC、PVDD |
Color |
Gray |
Golden |
Dark |
Silver |
Black |
HV |
3000 |
2400 |
2800 |
1850 |
4000-6000 |
Thickness |
1-4μm |
3μm |
2-5μm |
2-5μm |
1-2μm |
Coefficient of friction |
0.3 |
0.4 |
0.4 |
0.45 |
0.1 |
Process temperature |
450°C |
450°C |
450°C |
300-450°C |
200°C |
Resistant temperature to oxidation |
450°C |
550°C |
800°C |
700°C |
350°C |
RA surface roughness |
0.20 |
0.20 |
0.20 |
0.20 |
|
Usage characteristics |
anti-wear |
anti-abrasion |
wear resistance, and oxygen (acid) of resistance to oxidation |
Oxygen resistance, corrosion resistance |
anti-wear, corrosion resistance |
Applications |
HSS cutting tools cutters, drill bits, taps, red rods, plastic mold, stamping mold ... |
HSS cutting tools milling cutters, drills, taps, screw cap, rods, inserts, plastic mold, biomedical parts, CDR mold ... and so on. |
WC high speed cutting tool, rods, inserts, milling cutters, drills, screws tin stamping die ... and so on. |
Plastic mold, die casting, rubber mold, parts, tools ... and so on. |
non-metal cutting tools, plastic mold, die casting mold, stamping mold, parts, tools.. and so on. |
|
沒有留言:
張貼留言